News Feed
IARC7 Update November 27 2016
This is the first blog post to document the progress of the IARC Mission 7 team. Work began early in the Fall 2016 semester. We have an interdisciplinary team primarily consisting of students of mechanical, electrical, computer engineering, and computer science. This update will be structured to show progress of our primary subsystems.
Mechanical
The team is in the process of designing and building a custom airframe designed to meet IARC 7’s needs. All components are being modeled using the CAD tool Solidworks.
Two versions of the airframe are planned.
The first (V0.1), has been based off the commonly available X525 quadcopter frame and will be used to demonstrated proof of concept of our critical mechanical systems such as landing gear, prop guards, and mounts for the electronics. We are 3D printing a large majority of the components for V0.1 in order to encourage...
IARC7 Landing Gear Design Update November 27 2016
Purpose
Design landing gear capable of supporting impact for a 4kg drone dropped from a height of 2 meters while minimizing shock.
Design Concept – Cantilever Beam
A deflected beam acts like a spring and absorbs energy. This principle was the key idea behind the first landing gear design. Below is a diagram of a cantilever beam fixed on the left end, with a load “P” applied on the right end. Note the maximum deflection is at the tip of the beam on the right.

Applying this concept to drone landing gear, the cantilever beams are legs on the bottom of the drone which deflect from resultant force of impact to absorb the energy as illustrated below.
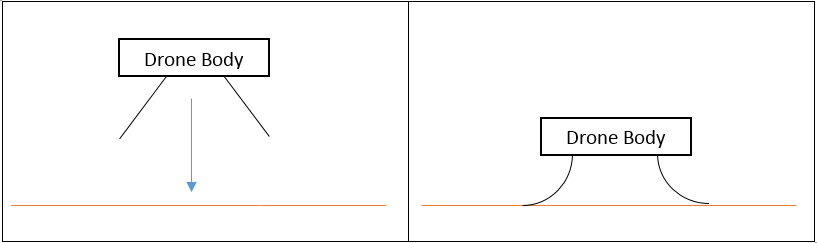
Therefore, to achieve the goal of dropping a drone without causing damage, the landing gear must be designed to absorb the energy from...
Newsletter October 2016
Michelle Riffitts assembled the RAS Newsletter for October 2016.
Workshops
Artbot
Motion Control
Scorpion
IARC 7